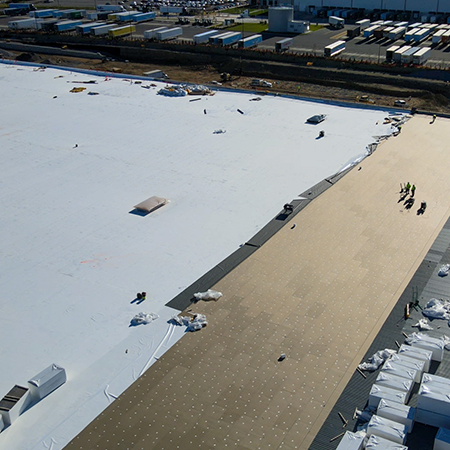
Commercial Roofers in The Bronx, NY
For over three decades, Tri-State Commercial Roofing Corp. has been known for our unmatched quality, reliability, and steadfast commitment throughout The Bronx, New York and beyond. As a family-owned and family-operated commercial roof company, we are committed to delivering unmatched service and expertise across the greater New Jersey, Connecticut, and New York Tri-State area. Bringing over 30 years of expertise to the forefront, we excel in overseeing commercial and industrial roofing projects of all types and sizes. We cover it all, including roof repairs, roof design, snow and ice removal, re-roofing, installation, various material and coating options, removal, maintenance, replacement, and restorations.
Stuart Roberts founded this company with a dedication to ensuring complete customer satisfaction, which has built enduring partnerships with contractors, property managers, and building owners across the northeast. Our skilled team guarantees top-tier roofs and an exceptional customer journey. Our team is fully OSHA-certified, ensuring safety is a priority at all job sites. As a licensed and insured company, we are certified by major roofing manufacturers such as Tremco, Firestone, Carlisle, Duro-Last, Versico, Johns Manville, Sika Sarnafil, Garland, GAF, Soprema, and more, providing a wide range of roofing systems tailored to meet the unique needs and budget of each project. As we enter our fourth decade of service, Tri-State Commercial Roofing Corp. reaffirms its commitment to delivering top-notch quality from beginning to end. Discover the dedication and excellence that set us apart.
Comprehensive Commercial Roofing Services
PVC Roofing
PVC (Polyvinyl Chloride) roofing offers flexibility, superior reflectivity, and the ability to block up to 90% of UV rays that degrade conventional flat roofing materials. Its resistance to ponding water is achieved through hot-air welding, resulting in a seamless, monolithic installation that enhances seam durability. PVC roofs help building owners save on cooling bills by minimizing heat absorption. In the opinion of our commercial roofers, PVC roofing stands out for its versatility, with options in many sizes, thicknesses, colors, and designs for flat and low-slope roofs.
Repairs
PVC roofing repair involves multiple steps to enhance the longevity and stability of your roof system. A skilled commercial roofer from Tri-State Commercial Roofing Corp. will begin by thoroughly cleaning the roof to remove debris, loose materials, and dirt, then proceed to cut out damaged sections of the membrane. After cutting a PVC patch to extend beyond the damaged area on all sides, we weld it onto the existing membrane. PVC roof repair is finalized through inspection and testing procedures to confirm the quality of fusion.
Replacement
PVC roof replacement begins by removing the existing roof, inspecting the deck for repairs, and completing other preparatory measures. During the The Bronx commercial roof replacement process, we roll out the PVC membrane and tailor it to fit precisely. We place and secure the sheets, weld the seams tightly to seal them against water, and incorporate flashings and edge features to safeguard against leaks. The final stage of PVC roofing replacement includes inspecting each component to ensure precise installation and proper sealing.
Advantages
Resistant to fire, chemicals, and wind
Highly functional
Reliable and efficient
Incredibly durable and strong
Helps reduce cooling costs by absorbing heat
Aesthetically pleasing
Resistant to ponding water
Suitable for heavy rain and snowfall
Built-Up Roofing
Modified bitumen roofing builds upon traditional asphalt methods by incorporating asphalt with solvents, rubber modifiers, and plasticizers. The typical installation process involves two methods: hot application, which means heating seams to meld the asphalt for a secure bond, and cold application, utilizing adhesives to adhere membrane sheets to the substrate and subsequent layers.
Repairs
The built-up roofing repair process starts with assessing for issues such as blisters, cracks, or loose gravel, followed by cleaning the affected area and applying new bitumen or adhesive as necessary. Seams and flashings are then inspected and repaired to prevent potential leaks. After completing the repairs, the roof is inspected to check waterproofing and adhesion. Our The Bronx commercial roof repair crew will then advise you to schedule regular maintenance to promote long-lasting durability.
Replacement
BUR (built-up roof) replacement involves removing the existing materials to uncover the roof deck, inspecting it thoroughly, and making any necessary repairs. Insulation might be added to boost energy efficiency. New layers of bitumen and fabrics are applied using either cold adhesives or hot asphalt. Commercial roof replacement involves employing sealants, flashing, and protective surfacing to achieve waterproofing. Upon completion, an inspection confirms adhesion and structural integrity. Ongoing maintenance and inspections post-installation are crucial for ensuring continued performance.
Advantages
Regular maintenance can lead to a lifespan of 20 years or more
Strong fire resistance that can be boosted with fire retardant additives
Durable
Cost-effective
Versatile
Reinforced and layered design allows for outstanding waterproofing and weather resistance
Reliable
Metal Roofing
Designed with panels made from aluminum or galvalume, metal roofing includes factory-made or site-formed components and incorporates a selection of flashing profiles. It is installed on roofs of different slopes, often selected for its ability to complement other roofing materials and architectural features. Featuring panels in various colors, metal roofing is adaptable for curved roof installations. It boasts a lifespan ranging from 40 to 70 years, contingent upon the metal type and surface coating selected.
Repairs
Metal roof repair begins with a detailed inspection to identify punctures, signs of corrosion, or dents. After this, surfaces are meticulously cleaned of rust, debris, and dirt in preparation for repairs. Minor problems are addressed with patches or sealants, while more extensive damage may necessitate the replacement of entire panels. Thorough inspection and repair of seams and flashings are crucial in preventing water damage. After metal roofing repair is completed, we ensure waterproofing efficiency and sealant adhesion. Routine maintenance is key to early issue detection, extending roof lifespan, and maintaining appearance and functionality.
Replacement
The process of metal roof replacement starts with the removal of existing flashing and panels to inspect the roof deck for any underlying damage, which is then repaired as necessary. This phase may include upgrading insulation to boost energy efficiency. Installing new galvalume or aluminum panels involves secure placement in accordance with the roof’s slope and design. Applying flashings and sealants is crucial for achieving waterproof integrity. A meticulous inspection is conducted to confirm installation accuracy and adherence to codes.
Advantages
Durable
Reduces cooling costs, minimizes heat absorption, and promotes energy efficiency
Lightweight
Highly resistant to mildew, rot, fire, and insects
Low maintenance
Exceptionally long lifespan of 40 to 70 years
Sustainable and 100% recyclable
Versatile and practical
EPDM Roofing
EPDM (Ethylene Diene Monomer), also known as rubber roofing, is a favored choice for commercial properties in the northeast. Its rubber-like flexibility, available in white or black, is well-suited for low-slope and flat roofs. It excels in resisting wind damage, fire, and harmful UV rays. Flashing and EPDM sheets are securely bonded with specific adhesives for lasting strength and durability.
Repairs
EPDM roof repair is typically straightforward, focusing on specific issues such as tears, leaks, or membrane seam separation. The process of EPDM roofing repair begins with a visual inspection of the roof or using advanced leak detection methods to identify and address any issues. Based on the findings of your skilled The Bronx commercial roofers, we’ll get to work cleaning affected areas, applying primer as needed, and/or applying patches or adhesives to damaged areas. Thorough execution of your commercial roof repair is pivotal to maintain membrane integrity and prevent future concerns.
Replacement
In the event that your current roof cannot adequately meet your requirements or has been damaged beyond repair, we’ll suggest an EPDM roof replacement. This process entails removing the existing EPDM membrane, preparing the roof substrate, and installing a new one. Our EPDM roofing replacement service delivers continuous protection, dependable performance, and warranty coverage. We advise regular commercial roof maintenance to maintain the integrity of your EPDM roof. Overall, EPDM roofing is a cost-effective, reliable, and versatile commercial roofing solution.
Advantages
Long lifespan
Easy installation for commercial roof contractors
Low maintenance
Energy-efficient
TPO Roofing
TPO (Thermoplastic Polyolefin) is widely utilized as a single-ply roofing membrane, notable for its high solar reflectivity similar to PVC. It boasts exceptional durability against tears, impacts, and punctures, installed in large sheets typically spanning 10 to 16 feet wide and reaching up to 100 feet long. It’s tailored to handle the temperature changes commonly found in The Bronx with its flexibility. TPO seams and flashings are fused using hot-air welding. Moreover, the material resists algae and is eco-friendly.
Repairs
TPO roof repair requires several essential procedures to ensure its durability and extended life. Initially, a thorough inspection identifies any damage such as seam failures, punctures, or tears. Then, the surface is cleaned to remove contaminants and dirt. In instances of minor issues, a PVC patch is cut to size and applied to the current membrane using a hot-air welder. More extensive or complicated repairs might involve replacing sections of the membrane. After completing the TPO roofing repair, we test the seams to ensure they are water-resistant. Regular maintenance inspections are necessary to extend the roof’s lifespan and prevent future commercial roof repairs.
Replacement
At the outset of TPO roofing replacement, we remove the current roofing material, including aged PVC membranes and any compromised insulation layers. The roof deck is inspected and repaired as needed to provide a stable base. Afterward, insulation is incorporated for improved energy effectiveness. Large sheets of fresh PVC membrane are rolled out and meticulously placed. Using hot-air welding, the seams are melded to form a seamless, waterproof surface. Flashings and edge details are welded to ensure extensive coverage and protection. Lastly, meticulous inspections validate adhesion and seam integrity, ensuring durability and longevity in the new TPO roof replacement.
Advantages
Stays flexible through temperature changes to avoid cracking
Durable enough to endure extreme weather conditions
Superior solar reflectivity absorbs minimal heat and helps cut down on energy costs
Resists impact, tears, and punctures
Hot-air welded seams provide a watertight, water-damage-resistant, seamless, and leak-resistant roof