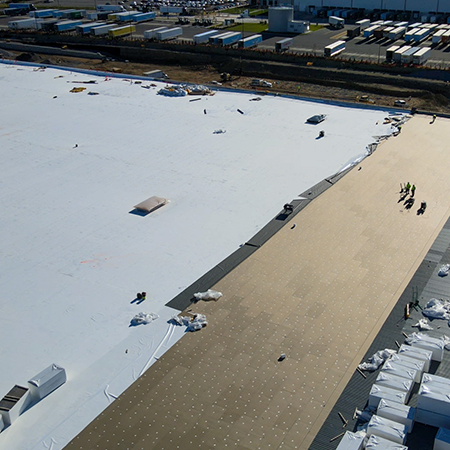
Commercial Roofers in Newburgh, NY
Tri-State Commercial Roofing Corp. is best known for our legacy of quality, reliability, and unwavering commitment, which has allowed us to grow and thrive in Orange County, New York and beyond for more than three unforgettable decades. As a family-owned, family-operated, and family-centered commercial roof company, we proudly serve the greater New York, New Jersey, and Connecticut Tri-State area with unmatched dedication and expertise. With over 30 years of experience, we have established ourselves as industry leaders in commercial and industrial roofing projects of all sizes. Our comprehensive range of services includes roof repairs, installation, maintenance, removal, replacement, roof design, restorations, re-roofing, snow and ice removal, and various material and coating options.
Stuart Roberts founded this company with a focus on total customer satisfaction, which has built enduring relationships with contractors, property managers, and building owners across the northeast. Our incredible team of experts ensures the highest quality roofs and an exceptional customer experience. Every team member is OSHA-certified, prioritizing safety on every job site. Our licensed and insured business is certified by major roofing manufacturers like Carlisle, Firestone, Soprema, Sika Sarnafil, Johns Manville, GAF, Versico, Duro-Last, Garland, Tremco, and more, offering a wide range of roofing systems tailored to each project’s needs and budget. As we enter our fourth decade in the business, Tri-State Commercial Roofing Corp. remains committed to delivering excellence from start to finish. We invite you to experience the dedication and quality that sets us apart.
Comprehensive Commercial Roofing Services
EPDM Roofing
EPDM (Ethylene Diene Monomer) roofing, commonly known as a rubber roof, is a popular commercial roof material for properties in the northeast. Available in black or white, this flexible, rubber-like material is ideal for flat and low-slope roofs. It offers exceptional resistance to fire, wind damage, and harmful UV rays. Seams between EPDM sheets and flashing elements are fused with specific adhesives to create a strong and durable bond.
Advantages
Long lifespan
Energy efficient
Low maintenance
Easy installation for commercial roof contractors
Repairs
The EPDM roof repair process is relatively straightforward, often addressing specific problems like membrane seam separation, tears, or leaks. An EPDM roofing repair begins with visually inspecting the roof and/or using advanced leak detection methods to identify any problems. Based on the findings of your skilled Newburgh commercial roofers, we’ll get to work cleaning affected areas, applying primer as needed, and/or applying patches or adhesives to damaged areas. It’s crucial to ensure that your commercial roof repair is done carefully to maintain the integrity of the membrane and prevent future issues.
Replacement
If we find that your old roof can no longer adequately meet your needs or is damaged beyond repair, we’ll recommend an EPDM roof replacement. During this process, the existing EPDM membrane is removed, the roof substrate is prepared, and a new one is installed. Our EPDM roofing replacement service guarantees continued protection, reliable performance, and a warranty. We also recommend routine commercial roof maintenance to keep your EPDM roof in tip-top shape. Overall, EPDM roofing is a cost-effective, reliable, and versatile commercial roofing solution.
PVC Roofing
PVC (Polyvinyl Chloride) roofing is flexible, highly reflective, and capable of blocking up to 90% of UV rays that can degrade other flat roofing materials. It is crafted to endure ponding water by utilizing hot-air welding, which creates a seamless, monolithic installation where the seams enhance the roof’s strength. PVC roofs also reduce heat absorption into buildings, effectively lowering cooling expenses. Available in a wide array of sizes, thicknesses, colors, and designs, our commercial roofers consider PVC roofing to be a versatile and suitable option for all types of flat and low-slope roofs.
Advantages
Absorbs heat for reduced cooling costs
Incredible strength and durability
Resistant to ponding water
Suitable for heavy rain and snowfall
Reliable and efficient
Resistant to wind, fire, and chemicals
Aesthetically pleasing
Highly functional
Repairs
PVC roofing repair involves many steps that ensure the longevity and integrity of your roofing system. Your expert commercial roofer from Tri-State Commercial Roofing Corp. will start by cleaning the roof to remove dirt, debris, and loose materials, then cut out damaged sections of the membrane. We’ll cut a compatible PVC patch that overlaps the damaged area on all sides, then weld the patch to the existing membrane. Your PVC roof repair will be completed after we inspect and test to ensure proper fusing.
Replacement
PVC roof replacement begins with the removal of the existing roof, an inspection of the deck and repairs as needed, and other preparatory steps. For this type of Newburgh commercial roof replacement, we roll the PVC membrane out and cut it to the correct dimensions. We position and secure the sheets, weld the seams to create a watertight seal, and install flashings and edge details for leak protection. The last step of the PVC roofing replacement process is to inspect every detail and ensure proper installation and sealing.
TPO Roofing
TPO (Thermoplastic Polyolefin) is a widely used single-ply roofing membrane, known for its high solar reflectivity similar to PVC. It is highly resistant to tears, impacts, and punctures, and is installed in large sheets, typically 10, 12, or 16 feet wide and up to 100 feet long. Its flexibility makes it well-suited for the temperature fluctuations common in the Newburgh region. TPO seams and flashings are hot-air welded. The material is also algae-resistant and environmentally friendly.
Advantages
High solar reflectivity for lower energy costs and minimal heat absorption
Flexibility to withstand temperature fluctuations without cracking
Resistant to tears, impact, and punctures
Long-lasting durability, even in harsh weather
Hot-air welded seams for a seamless, watertight, leak-resistant, and water-damage-resistant roof
Repairs
TPO roof repair involves several key steps to ensure durability and longevity. First, a thorough inspection identifies damage such as punctures, tears, or seam failures. The surface is then cleaned to remove dirt and contaminants. For smaller issues, a PVC patch is cut to size and fused to the existing membrane with a hot-air welder. Larger or more complex repairs may require replacing sections of the membrane. After the TPO roofing repair is done, the seams are tested for watertightness. Regular maintenance checks can extend the roof’s lifespan and prevent future commercial roof repairs.
Replacement
The first step of the TPO roofing replacement process is removing the existing roofing material, including old PVC membranes and damaged insulation layers. The roof deck is inspected and repaired as needed to provide a stable base. Insulation is then added to improve energy efficiency. Large sheets of new PVC membrane are rolled out and positioned carefully. Using hot-air welding, the seams are fused together to create a seamless, watertight surface. Flashings and edge details are also welded for comprehensive coverage and protection. Finally, thorough inspections confirm proper adhesion and seam integrity, ensuring the TPO roof replacement is resilient and long-lasting against various weather conditions.
Built-Up Roofing
Modified bitumen roofing has evolved from traditional asphalt roofing methods. It consists of asphalt combined with rubber modifiers, plasticizers, and solvents. Installation typically involves two methods: hot application, where seams are heated to fuse the asphalt for a strong bond, and cold application, which uses adhesives to attach the membrane sheets to the substrate and subsequent layers.
Advantages
Durable
Lifespan of 20 years or more with proper maintenance
Good fire resistance (which can be further enhanced by fire retardant additives)
Reinforced and layered design provides excellent weather resistance and waterproofing
Versatile
Reliable
Cost-effective
Repairs
Built-up roofing repair involves inspecting for damage like cracks, blisters, or loose gravel, cleaning the area, and applying new bitumen or adhesive as needed. Flashings and seams are checked and repaired to prevent leaks. After repairs, the roof is inspected for adhesion and waterproofing. Our Newburgh commercial roof repair team will then recommend regular maintenance for long-term durability.
Replacement
BUR (built-up roof) replacement involves removing existing materials to expose the roof deck, then inspecting and repairing it as needed. Insulation may be added for energy efficiency. New layers of bitumen and fabrics are applied with hot asphalt or cold adhesives. Flashings, sealants, and protective surfacing ensure waterproofing. To conclude the commercial roof replacement process, an inspection confirms adhesion and structural integrity. Maintenance and inspections post-installation are crucial for long-term performance.
Metal Roofing
Metal roofing consists of factory-made or site-formed panels, typically made of galvalume or aluminum, along with flashing profiles. It is installed on low-sloped or steep-sloped roofs and is often used for architectural accents alongside other roofing systems. Panels come in various colors and can be installed on curved roof areas. Metal roofing boasts an impressive lifespan of 40 to 70 years, depending on the metal type and surface finish chosen.
Advantages
Durable
Exceptionally long lifespan of 40 to 70 years
High resistance to rot, mildew, insects, and fire
Low maintenance
Lightweight
Practical and versatile
Minimizes heat absorption, reduces cooling costs, and contributes to energy efficiency
Environmentally friendly and fully recyclable
Repairs
Metal roof repair involves an inspection to pinpoint dents, punctures, or corrosion. The next step is surface preparation, which cleans surfaces of dirt, debris, and rust. For minor issues, we use sealants or patches, while larger ones might call for the replacement of panels. Flashings and seams are inspected and repaired to prevent water damage. After the metal roofing repair is completed, we confirm sealant adhesion and waterproofing. Regular maintenance can detect issues early, extend your roof’s lifespan, and preserve functionality and appearance.
Replacement
Metal roof replacement begins with removing existing panels and flashing to inspect the roof deck for damage, then repair any problems that are uncovered. Insulation may be upgraded at this point for energy efficiency. New galvalume or aluminum panels are installed securely, while accounting for the roof’s slope and design. Flashings and sealants are applied to ensure waterproofing. A thorough inspection is the last step, which confirms installation quality and adherence to codes.
For all your commercial roofing needs, turn to Tri-State Commercial Roofing Corp. Give us a call today at (845) 362-1730 to learn more!